0 items | $0.00
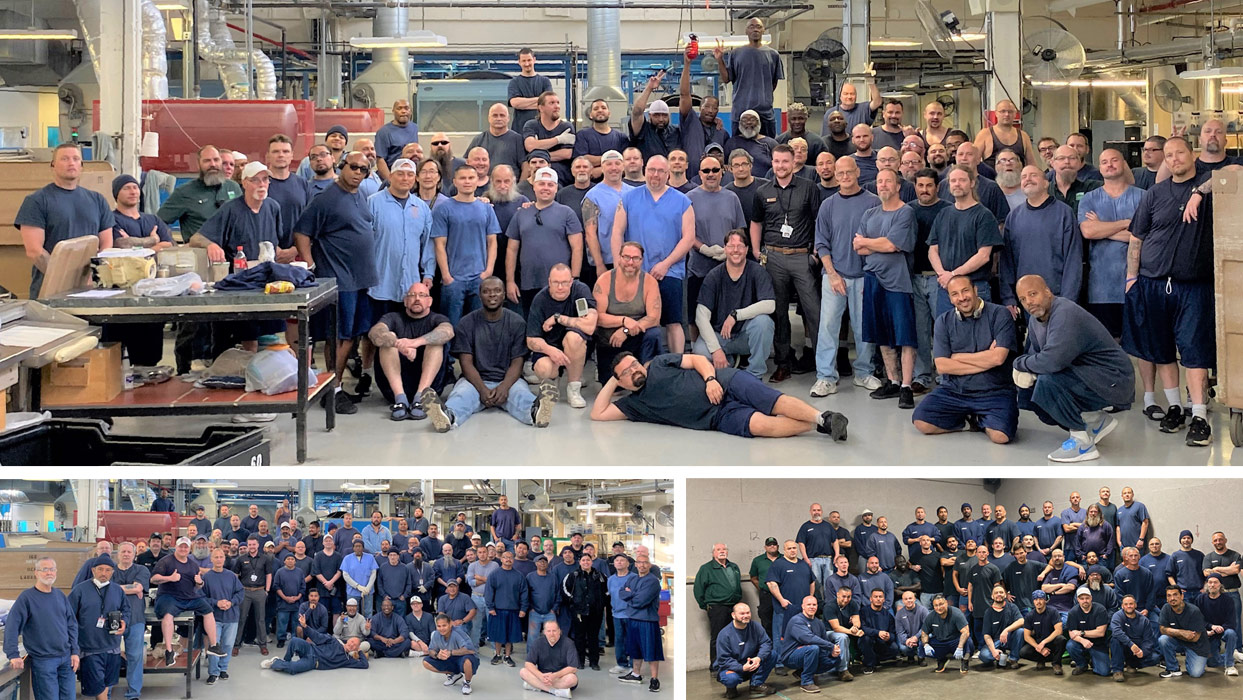
06/30/2023
In late January, OCE laundry at OSP was approached by one of our partners, they had some major machinery issues causing their tunnel washers to stop operating as well as some significant issues with their dryer units. This affected their capabilities to produce clean linen for their customers. They asked if we would be willing to take on some additional weight to what they were already sending us, during the peak linen season (winter). After some negotiations, we agreed to take on the additional work and began processing linen so patients would not go without. To date, the OSP laundry has processed a total of 489,338 lbs. of extra linen. And laundry sort has handled 3,888 extra laundry carts.
The team stepped up and worked tirelessly to not only produce clean linen on time for our normal commitments, but also stay ahead of schedule on this added work. A few numbers to wrap it all into perspective: There have been 1,014,215 bath blankets, 212,651 fitted sheets, 494,967 scrub pieces, and 1,601,375 flat sheets processed since the end of January when this all began. Not included in that number is the number of gowns, specialty items, baby linen, institution linen, and much more.
When we look at the national average for a metric called "Pounds per Adjusted Patient Day" (PAPD) we see that the industry average is about 15.5 PAPD. This means that the OSP Laundry was able to produce 31,570 days' worth of patient linen in addition to what we are committed to processing, this is an astonishing amount! This could not have been accomplished if it was not for the coordination and collaborative efforts from both our staff and AIC crews, especially our leads.
We would like to recognize some of the key people who made this a success.
Robert W. has worked for OCE Laundry for 14 years. He is currently the lead person for the receiving end of the laundry. He has held this position for 6 years. He has been a big part of helping process the add weight brought on by our partner. He has been willing to work extra shifts as needed to help the team achieve its goals. He always comes to work with a good attitude and has a good working relationship with staff and his co-workers.
On the receiving end, Lovene G. helps a ton on the Saturdays when we do not have lead worker signed up. Lovene has helped organize the tunnel schedule and made our work go much more smoothly than it might have been without their guidance.
Edward G. and Matt R., our floor leads have stepped up during the week to act as traffic controllers in our laundry, often navigating changing wash order. During this time of added work, many changes were made outside of the laundry's control, these individuals stepped up, collaborated with staff and provided fluidity between each section and their corresponding production coordinator that was essential for their corresponding shift.
Mark L. is a huge part of the laundry's success. His ability to organize and keep track of product moving through the laundry is unmatched. He is the lead scale operator on swing shift shipping. With added production the need to keep the scale area running efficient and with few mistakes is a time saver. He will work loading trucks on the shipping dock and folding gowns as the need arises. His dedication to making sure it's done right has save me many miles of running around. Mark is humble with his work, but his work speaks volumes.
Alby S. and Jose F. have been amazing help during our increased work. The have worked well together building an efficient and effective team. They have adapted to each change we have had to make while continuing to have positive attitudes.
Alfredo H., our blanket blaster lead he has worked well with the uptick in production and has been a great team leader. He has gone above and beyond to ensure the effectiveness of his team. He's led meetings with his group to ensure production goals are met, in a timely manner proving him to be invaluable to his team as well as the laundry.
Norman G. and Jeremy S., our towel section leads and their teams have efficiently taken on the added work in their section. Just the sheer amount of terry product going through their area during normal production is something commendable, but with the added work their efforts are truly exemplary!
Arturo G. is our dayshift special fold lead. His team continues to do an amazing job, they jump in and help where they see it is necessary with things like the overflow items from blanket blaster and scrubs. He maintains a positive attitude and his team has caught on to his contagious demeanor building morale with his team and staff alike.
Brent R., Alcibiades B., Miguel Q., Arturo G., Hunter A., and Julio A. our dayshift and swing shift leads in our folding sections have helped their teams navigate the extra workload. Often times, the folding areas work so far ahead, that they are able to take on work from other areas. To provide assistance with the extra work these leads have often volunteered to process items, such as bath blankets, fitted sheets, scrubs or overflow carts to ensure the completion of contracts for other areas.
Chad R., Santos A., and Korey E. our leads in the scrub areas have proved that their attention to detail and willingness to take on more-than-they-asked-for is an asset to their team and the laundry at large. There have been times during this inflated work load (the amount of scrubs needing to be processed) had nearly quadrupled, without complaint they ensured that scrubs for all customers were maintained, kept separate and completed on-time for our hospital partners. They are keen on providing a quality product, every time.
Cristobal G. has been a big help to the laundry during this time of added production. He is the ironer lead in charge of keeping two industrial irons running at maximum capacity. His ability to organize and motivate his crew to produce record numbers consistently has helped the laundry reach its goals. When customers added new product to the peak season he stayed over to lead a late crew to complete the job.
Marc N., Sean J. and Edward H., our shipping clerks worked tirelessly to ensure paperwork was lined up and ready for billing. Even as production carries the laundry, these clerks are handed many backend projects where completion is vital for our success. Ensuring our established processes align with new processes and the paperwork is a match. They provide a necessary check and balance to our already complex operation.
Jeffery W. and Robert C. are two maintenance super stars. They have been providing top quality maintenance support during our increased workload. Jeffery is currently our lead worker, he stepped into the roll after our last lead was released. He has done a great job in the position. Robert has been in maintenance for a while. His skill set is primarily mechanical, but he is handy in many other areas. Between the two our maintenance shop has managed to keep the machines moving along, even with an elevated workload. Most maintenance workers are working on Saturdays to assist, but in the production areas. If the reactive maintenance needed is serious enough, the other workers assist with the repair work then return to their assigned production work area. Their flexibility is greatly appreciated.
Our production coordinators Eric Zehner, Bryan Derksen, Benjamin Noid and Cheyenne Gutierrez played an integral part in supervising the flow of linen, managing the AIC workers and maintaining a positive work environment during this time. They also took on overtime shifts on Saturdays to keep up with the added work, they have worked a total of 260 hours on Saturdays since the beginning of this project. Our production coordinator at laundry sort Josh Phillis has managed the incoming linen deliveries, aligned AIC workers, and ensured the laundry was constantly receiving soiled linen to process. Our customer service coordinators Gary Bradley, James Erpelding, Greg Lindgren, Dawayne Eacret, Mark Taylor and Bryan Baker have stepped up and have handled nine extra deliveries to customers in local proximity to us and worked a total of 207.5 hours on Saturdays. Our industrial maintenance electrician Shawn Findley has worked with our AIC maintenance group to ensure our machines do not fail during this increased workload.
This has truly been a collaborative team effort to make this tremendous achievement possible. We could not be more proud of the work you all do.
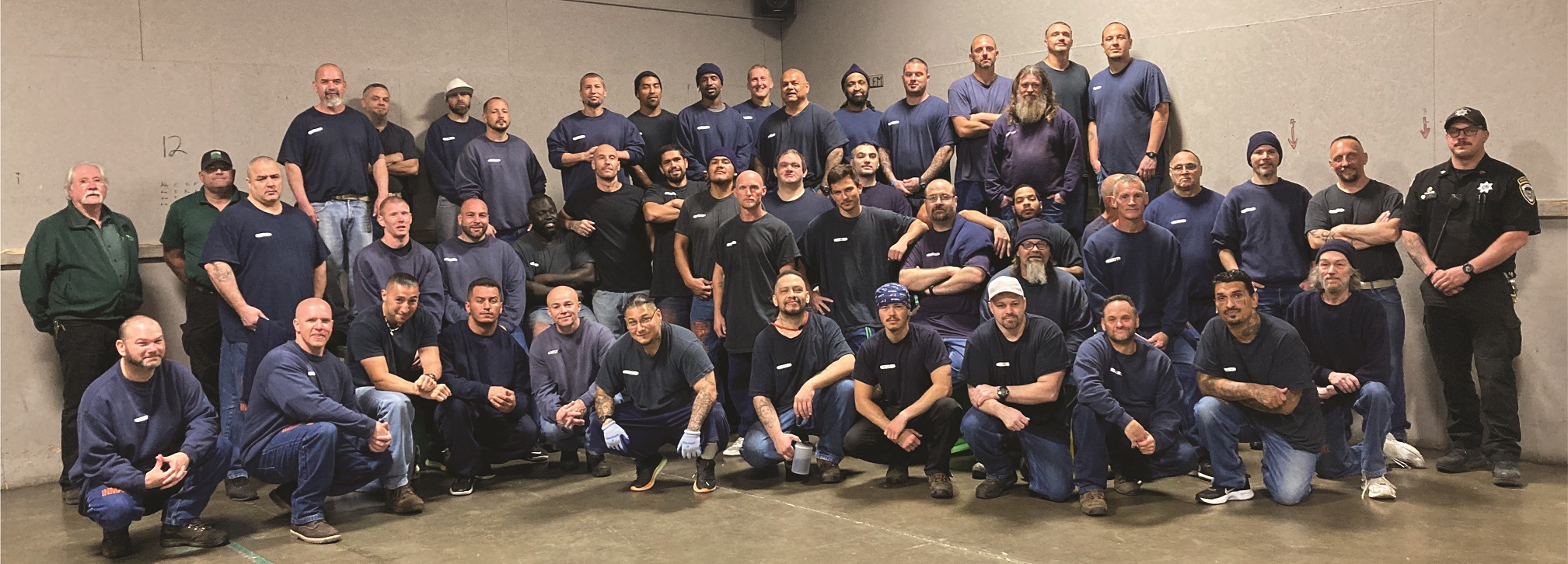
When we look at the national average for a metric called "Pounds per Adjusted Patient Day" (PAPD) we see that the industry average is about 15.5 PAPD. This means that the OSP Laundry was able to produce 31,570 days' worth of patient linen in addition to what we are committed to processing, this is an astonishing amount! This could not have been accomplished if it was not for the coordination and collaborative efforts from both our staff and AIC crews, especially our leads.
We would like to recognize some of the key people who made this a success.
Robert W. has worked for OCE Laundry for 14 years. He is currently the lead person for the receiving end of the laundry. He has held this position for 6 years. He has been a big part of helping process the add weight brought on by our partner. He has been willing to work extra shifts as needed to help the team achieve its goals. He always comes to work with a good attitude and has a good working relationship with staff and his co-workers.
On the receiving end, Lovene G. helps a ton on the Saturdays when we do not have lead worker signed up. Lovene has helped organize the tunnel schedule and made our work go much more smoothly than it might have been without their guidance.
Edward G. and Matt R., our floor leads have stepped up during the week to act as traffic controllers in our laundry, often navigating changing wash order. During this time of added work, many changes were made outside of the laundry's control, these individuals stepped up, collaborated with staff and provided fluidity between each section and their corresponding production coordinator that was essential for their corresponding shift.
Mark L. is a huge part of the laundry's success. His ability to organize and keep track of product moving through the laundry is unmatched. He is the lead scale operator on swing shift shipping. With added production the need to keep the scale area running efficient and with few mistakes is a time saver. He will work loading trucks on the shipping dock and folding gowns as the need arises. His dedication to making sure it's done right has save me many miles of running around. Mark is humble with his work, but his work speaks volumes.
Alby S. and Jose F. have been amazing help during our increased work. The have worked well together building an efficient and effective team. They have adapted to each change we have had to make while continuing to have positive attitudes.
Alfredo H., our blanket blaster lead he has worked well with the uptick in production and has been a great team leader. He has gone above and beyond to ensure the effectiveness of his team. He's led meetings with his group to ensure production goals are met, in a timely manner proving him to be invaluable to his team as well as the laundry.
Norman G. and Jeremy S., our towel section leads and their teams have efficiently taken on the added work in their section. Just the sheer amount of terry product going through their area during normal production is something commendable, but with the added work their efforts are truly exemplary!
Arturo G. is our dayshift special fold lead. His team continues to do an amazing job, they jump in and help where they see it is necessary with things like the overflow items from blanket blaster and scrubs. He maintains a positive attitude and his team has caught on to his contagious demeanor building morale with his team and staff alike.
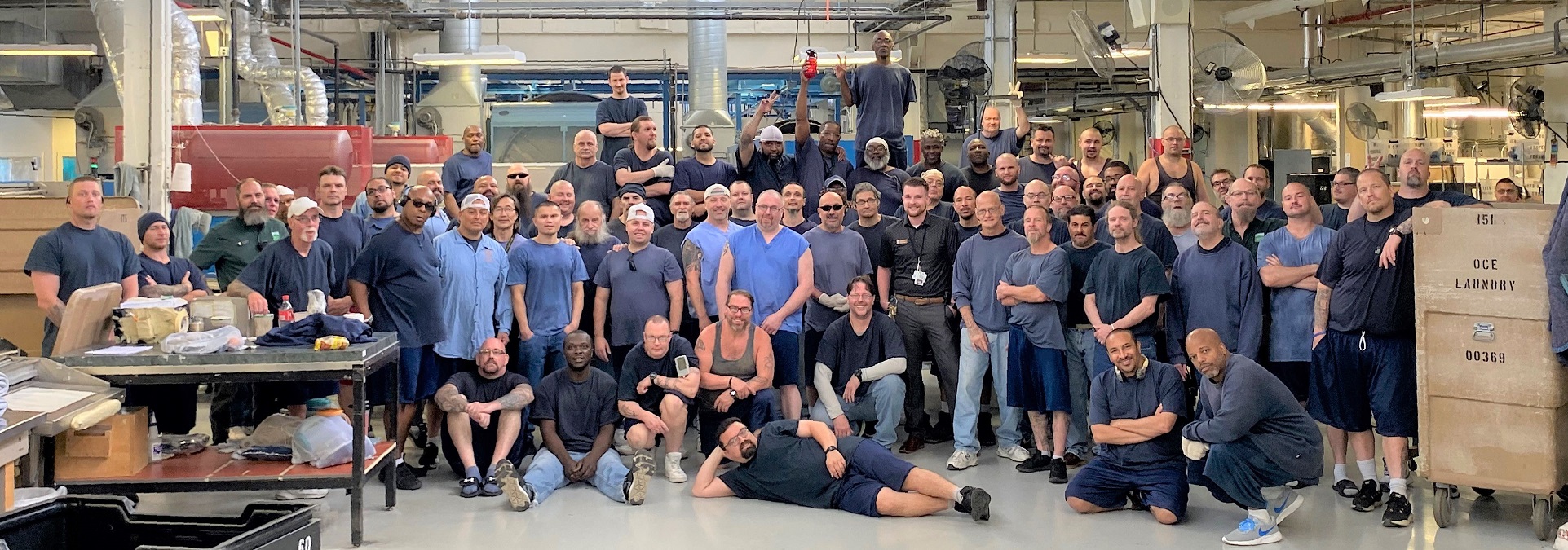
Chad R., Santos A., and Korey E. our leads in the scrub areas have proved that their attention to detail and willingness to take on more-than-they-asked-for is an asset to their team and the laundry at large. There have been times during this inflated work load (the amount of scrubs needing to be processed) had nearly quadrupled, without complaint they ensured that scrubs for all customers were maintained, kept separate and completed on-time for our hospital partners. They are keen on providing a quality product, every time.
Cristobal G. has been a big help to the laundry during this time of added production. He is the ironer lead in charge of keeping two industrial irons running at maximum capacity. His ability to organize and motivate his crew to produce record numbers consistently has helped the laundry reach its goals. When customers added new product to the peak season he stayed over to lead a late crew to complete the job.
Marc N., Sean J. and Edward H., our shipping clerks worked tirelessly to ensure paperwork was lined up and ready for billing. Even as production carries the laundry, these clerks are handed many backend projects where completion is vital for our success. Ensuring our established processes align with new processes and the paperwork is a match. They provide a necessary check and balance to our already complex operation.
Jeffery W. and Robert C. are two maintenance super stars. They have been providing top quality maintenance support during our increased workload. Jeffery is currently our lead worker, he stepped into the roll after our last lead was released. He has done a great job in the position. Robert has been in maintenance for a while. His skill set is primarily mechanical, but he is handy in many other areas. Between the two our maintenance shop has managed to keep the machines moving along, even with an elevated workload. Most maintenance workers are working on Saturdays to assist, but in the production areas. If the reactive maintenance needed is serious enough, the other workers assist with the repair work then return to their assigned production work area. Their flexibility is greatly appreciated.
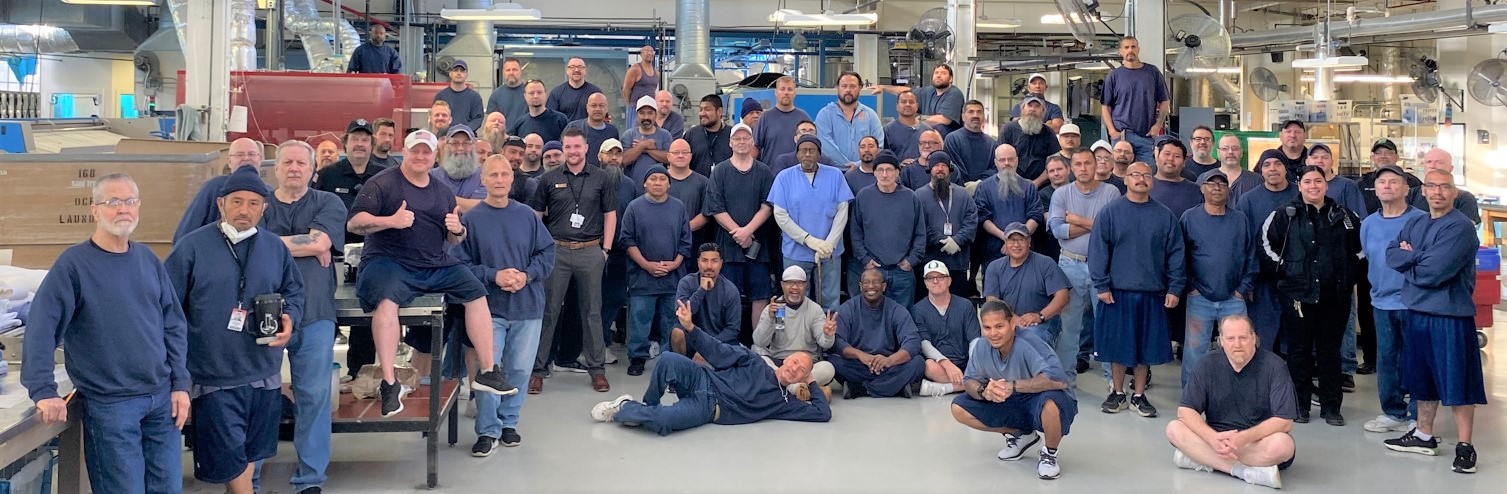
This has truly been a collaborative team effort to make this tremendous achievement possible. We could not be more proud of the work you all do.
Posts by Category
Monthly Archive